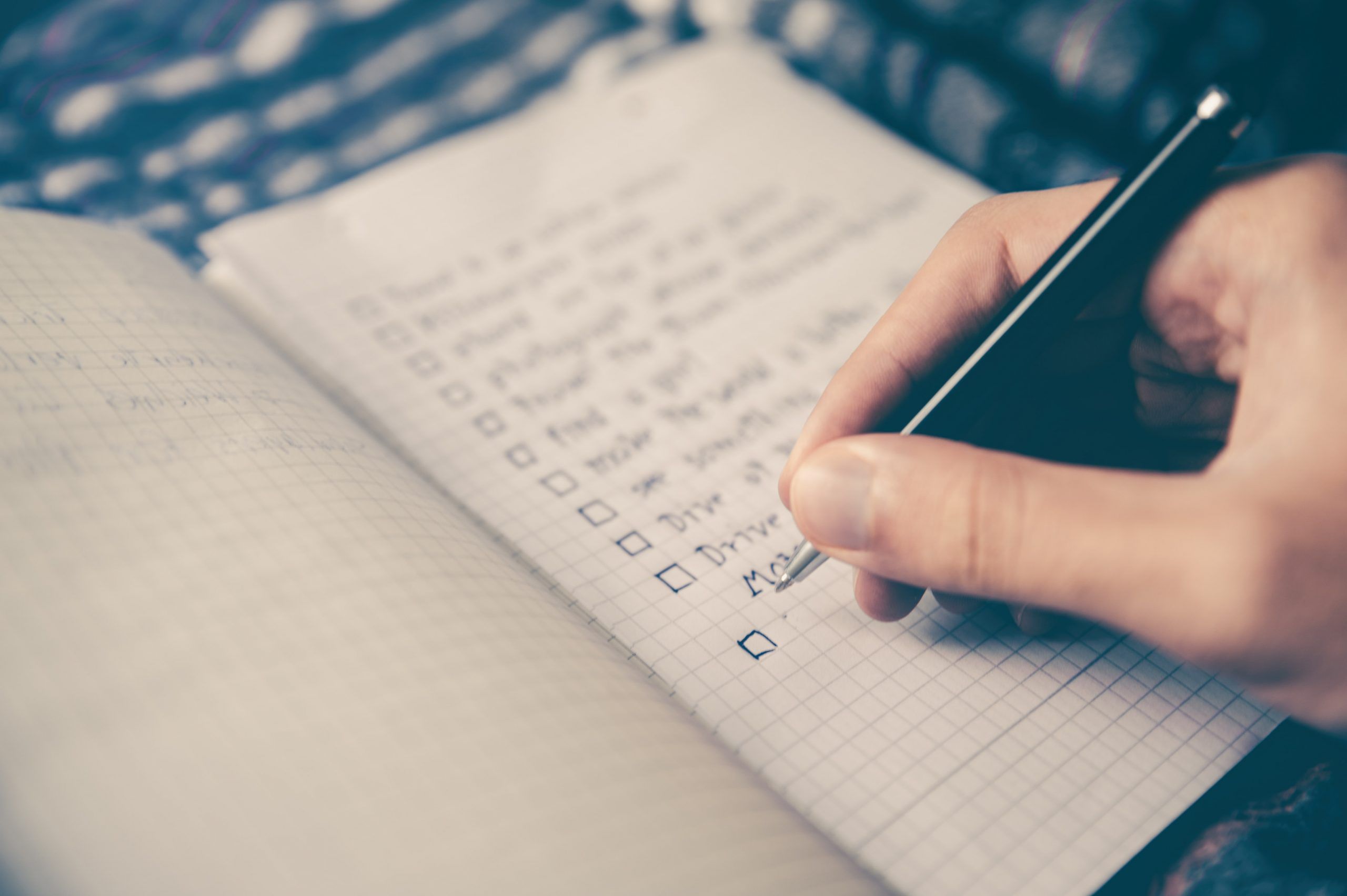
Why You Should Take a Proactive Approach to Hard Facilities Management
Hard facilities management is the term used when referring to the physical structure of a building and the facilities which cannot be removed. In other words, the facilities that are required, by law, for the safety and welfare of people in the building. This includes building maintenance work, HVAC systems, lighting, gas, plumbing, electrics and more.
This is different to soft facilities management, which deals with things like decorating, cleaning and waste management. Basically, the things that can make a space nicer to be in, but isn’t absolutely essential like those in the hard facilities category.
Some facilities bridge both areas, such as landscaping. For the physical structure itself, such as paths and walls, it would be hard facilities management. For plants and other decorative features, however, this would come under soft facilities management.
It is worth noting that a lot of maintenance will need to be carried out on a planned basis, purely to follow legislations. This post isn’t about the maintenance that you have to carry out to follow the law, but the benefits of taking a proactive approach to your asset management, rather than waiting for assets to break.
Reactive Facilities Management
Taking a reactive approach to facilities management is the equivalent to always having to put out fires, rather than spotting the fire hazards in the first place. Equipment is just left to run until it breaks, at which time it will have to be repaired or replaced.
There are many issues with reactive FM:
- Waiting for an asset to break almost guarantees downtime. This can lead to businesses having a decrease in productivity, costing them time and money. In educational facilities this could mean a loss of valuable time for learning, which can be a nightmare for parents to arrange for their children to be picked up. The knock-on effects can be tremendous.
- An asset’s life expectancy will be dramatically reduced if you are not routinely performing maintenance on it. Manufacturers will design their products with the intention of them being maintained appropriately to ensure their customers get the full life out of them.
- Assets unexpectedly reaching their end of life can seriously affect planned budgets. Emergency repairs can cost up to 40% more than taking a proactive approach with regular maintenance.
- It may seem like you are saving money by neglecting to replace small components, not lubricating moving parts or refusing to pay for maintenance staff. However, in the long term, you will generate much higher costs. For example, you may have to replace a whole system rather than one small part.
- Dealing with broken assets can be stressful if replacing them is urgent. It can disrupt a facility manager’s daily routine and get in the way of important tasks, such as maintenance that is required by a certain date to follow legislations.
Proactive Facilities Management
Taking a proactive approach to maintenance is when you plan regular checks on equipment to ensure it is running efficiently and that there are no major issues that could cause it to break. This approach is also known as preventative maintenance as it does just that. It prevents major issues happening in the first place. If there’s no kindling, there’s no fire to put out!
One easy way to think about how this approach is better is by imagining a specific piece of equipment. For example, let’s say you have an air conditioning unit on your premises. Would it be faster, easier and cheaper to check it once every couple of months to see if it is overheating or making excessive noise? Or would it be better for it to break? Call in emergency maintenance, see if it can be fixed, potentially buy a replacement and wait for it to be installed? It’s far less stressful to stay on top of maintenance rather than running around trying to fix everything as and when they inevitably fail.
The benefits of proactive FM include:
- It is far easier to plan costs, as you will know when maintenance is happening, rather than having to fork out large sums for emergency repairs/replacements.
- Equipment will last a lot longer and at a higher efficiency, saving money on replacing end of life equipment and on energy bills.
- Minimise the risk of downtime based on asset deterioration.
- Buildings will be kept to a higher standard, making sure they are constantly fit for purpose. Obviously, this is good for the people that use the building on a day-to-day basis as they will have a better experience and most importantly, a safer one too.
So, it is clear now that you should be utilising planned preventative maintenance (PPM), how should you make a plan?
Types of preventative maintenance
There are several different methods for carrying out preventative maintenance. These include time-based, usage-based and failure-finding. All three of these can be effective methods, although they are typically reserved for different types of equipment/areas of a structure.
Time-based maintenance is generally used for equipment that is essential for the building to operate. This is planned maintenance that can be carried out anywhere from daily to annually, depending on how important equipment is and how prone to failure it is. This is also generally scaled on the age of an asset too. Manufacturers provide guidance on how often maintenance should be carried out throughout the asset’s life to ensure it achieves its target life expectancy. This method is great for prioritising, allowing you to save time and resources.
Usage-based maintenance is used for assets that are used very regularly by employees. These assets tend to be what we would refer to as soft facilities, such as cars, or production machines in a factory. They will be checked every 5,000 miles driven, or after operating for 1,000 hours, for example.
Finally, there is Failure-Finding Maintenance. This is a regular inspection of an entire site, or part of a site at a time. It is used to discover any failures or defects that could lead to failures. This is a great method for discovering faults outside of when assets are due to be checked.
Typically for hard facilities management, the best approach is a mixture of time-based maintenance and failure-finding maintenance. This ensures that assets are checked regularly, especially the most important ones, whilst keeping overall time and resources minimal.
What we do
Obviously, we are only scratching the surface of what you need to consider for facilities management. There’s a lot to cover and it can be hard to stay on top of maintenance especially when you need to spend time hitting legislation dates, co-ordinating various suppliers and ensuring on-site staff’s time is organised to work alongside those PPM schedules. Munday + Cramer have a lot of experience in this field and provide hard facilities management services to extremely high standards. We do this to ensure the safety and wellbeing of people in our clients’ buildings. We provide these services across all sectors, from educational buildings, such as schools and colleges, to offices, retail buildings, hotels, hospitals, churches and beyond.
We work with our clients to understand their properties, carrying out condition surveys and create asset management plans. These will help to create maintenance plans which, along with our compliance tool, will allow them to stay on top of building maintenance, saving time and money in the process. Alternatively, we can create the plan for our clients, help organise work to get assets up to standard and manage audit trails on their behalf, via our facilities management offering.

Contact Us
Proactive, planned hard facilities management is the best approach. For information on how Munday + Cramer can help in this process, or if you’d like to find out more about our building surveying services, operating in Essex, London, Kent, Norfolk and Suffolk, then get in touch! Contact Munday + Cramer today on 01245 326 200.