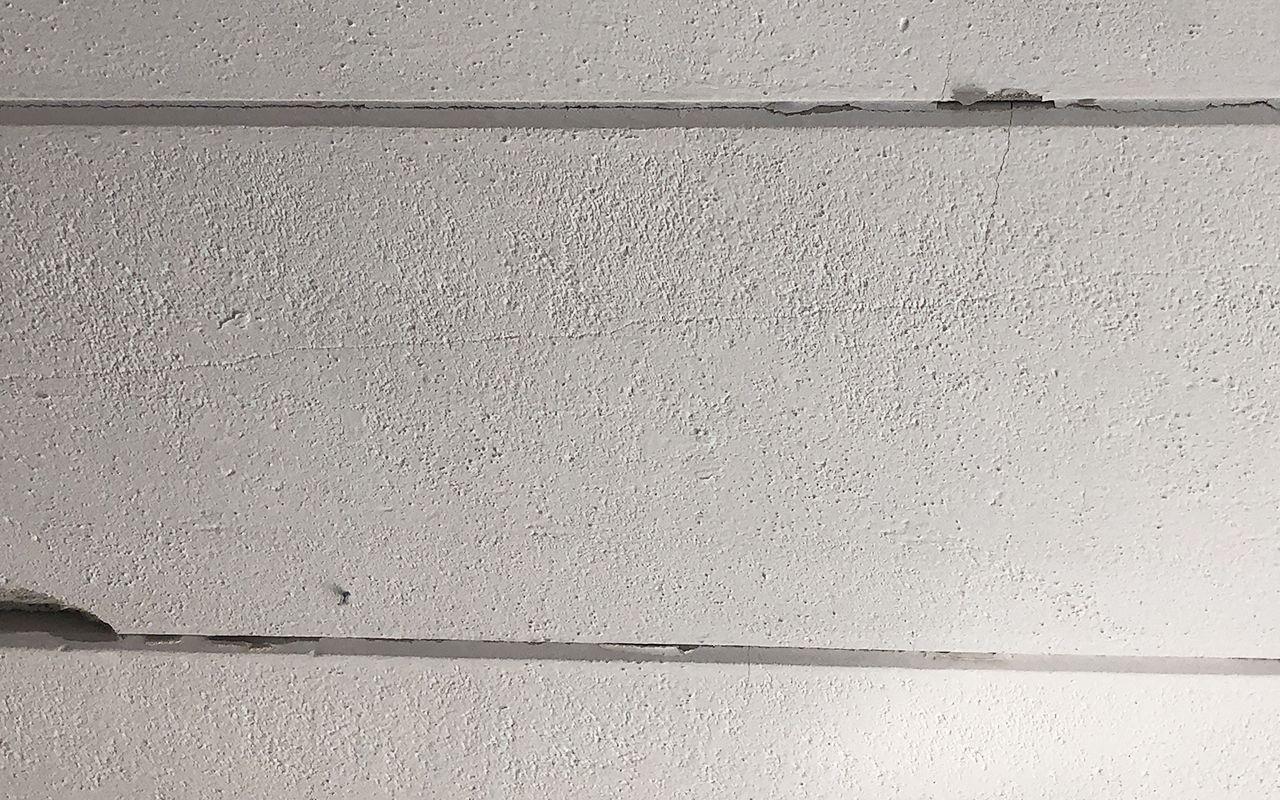
Reinforced Autoclaved Aerated Concrete (RAAC) – What you need to know
Reinforced Autoclaved Aerated Concrete (RAAC) has been a widely talked topic within the built environment for a number of years. Any organisation with buildings constructed between the 1950’s and 1980’s will potentially feature this material within its construction. Sadly, the degradation of the material has resulted in the failure of a number of buildings within the UK and further afield. What’s more, some of these cases have been catastrophic. These fears have led to a major review of the material and its applications in buildings across the UK. The NHS alone estimates that repairs to thirty hospitals will cost in the region of £1 billion. Additionally, there are thought to be around 1,500 schools that were constructed at the height of RAAC usage. Here we will provide you with further information about the material, its uses, and the road map forward for managing and mitigating its inherent risks.
What is RAAC?

Reinforced Autoclaved Aerated Concrete (RAAC) is a versatile and sustainable building material. It gained popularity in the 1950’s due to its lightweight, thermal insulation properties, and eco-friendly characteristics. The development of Autoclaved Aerated Concrete (AAC) can be traced back to the early 20th century. AAC was initially invented in Sweden in the 1920’s and gained significant attention in Europe due to its low density and ease of use. Over time, advancements led to the introduction of Reinforced Autoclaved Aerated Concrete (RAAC). This incorporated steel reinforcement to enhance its structural integrity. RAAC is made by mixing cement, sand, lime, and aluminium powder with water. This produces a lightweight, porous material that is strong and resilient.
It is important to note that although it is named ‘concrete’, it actually isn’t!
It has been used extensively in Europe, Asia, and Australia, and with the continued improvement and refining through the years, RAAC is one of the most popular building materials in the construction industry.
The problem with RAAC

Large planks of Reinforced Autoclaved Aerated Concrete are formed by a ‘foaming’ process that combines silicate and calcareous chemicals as well as bulking and accelerating agents. The foamed material is designed to be bonded to the reinforcement to gain its structural integrity.
However, planks can deflect between bearing points because of several environmental factors including loading, moisture penetration and thermal/carbon influences. Deflection can cause cracking where the AAC material is over-stressed, or where it fails around reinforcement. This cracking also allows moisture penetration which in turn, can weaken the reinforcement itself.
The Building Research Establishment (BRE) conducted numerous studies into the design, application, and performance of RAAC (and AAC) materials and their published papers IP10/96 and IP7/02 set out highly detailed performance data based on extensive destructive tests. BRE advise it is essential to establish the adequacy of the bearing points, extent and nature of deflection, position and cover of the reinforcement and potential influences on the stability of the planks (e.g. roof leaks that might cause deterioration of the aerated planks or their bonding to the reinforcement).
Risks associated with Reinforced Autoclaved Aerated Concrete

The composition and manufacture of Reinforced Autoclaved Aerated Concrete brings about a number of risks to structures, which
- Structural Integrity: While RAAC offers strength and durability, improper design, construction, or reinforcement installation can compromise its structural integrity. In rare cases, this can lead to structural failures, such as collapse or cracking of walls, floors, or roofs. These incidents can pose severe risks to occupants and nearby properties.
- Fire Resistance: RAAC is inherently fire-resistant but its specific composition and the presence of organic binders can affect its fire performance. If substandard or low-quality RAAC is used it may not provide adequate fire protection, potentially endangering the building’s occupants and neighbouring structures.
- Moisture and Water Damage: RAAC is susceptible to moisture penetration if not properly sealed or protected. Water ingress can cause material degradation, weakening the structure over time. This can lead to mould growth, deterioration of finishes, and potential health hazards for occupants.
Examples of Incidents:
While RAAC is generally considered safe, a few examples highlight the risks associated with improper implementation:
- In 2018, Singlewell Primary School suffered the collapse of the roof structure in a number of areas, all of which were constructed from RAAC. Fortunately the incident occurred over a weekend, causing no casualties.
- In 2016, a residential building in India constructed using RAAC collapsed, causing multiple fatalities. Investigations revealed structural deficiencies and a lack of adherence to construction standards as contributing factors.
Mitigation Strategies
Whilst major incidents have occurred, RAAC within a property can be managed effectively, so long as it is well maintained and not allowed to degrade significantly. To minimise the risks associated with RAAC construction, the following measures should be implemented:
- Proper Design and Engineering: Engage experienced architects, engineers, and contractors who have expertise in RAAC construction to review the existing RAAC construction. Undertake adequate structural analysis, and carry out reinforcement where necessary to ensure the building’s stability and safety.
- Quality Assurance: Use high-quality RAAC blocks, reinforcement materials, and construction practices. Regular inspections and testing should be conducted to ensure compliance with industry standards.
- Fire Protection Measures: Adhere to fire safety regulations and utilise appropriate fire-resistant coatings or treatments to enhance the fire performance of RAAC structures. Install fire alarms, sprinkler systems, and evacuation plans to minimise fire-related risks.
- Moisture Management: Implement comprehensive waterproofing measures during construction. You should pay particular attention to joints, openings, and critical areas prone to moisture infiltration. Regular maintenance and inspections should be carried out to identify and rectify any signs of water damage. This includes ensuring that roof coverings are adequate, and not suffering damage/leaks which could penetrate the RAAC structure.
RAAC is a versatile and durable building material that does have many benefits. However, it also has significant risks that must be addressed to ensure the safety of the properties and its users. The prevalence of the material in public sector buildings only exacerbates the level of impact that the material has across the UK. By implementing proper installation, maintenance, and mitigation measures, the risks associated with RAAC are significantly reduced. This will ensure that it remains a safe and reliable building material for years to come.
Contact Us
Munday + Cramer can assist you in reviewing your exposure to Reinforced Autoclaved Aerated Concrete within your buildings and will undertake an initial exploratory survey. For more information, call us today on 01245 326 200 or just click here.
architects in Chelmsford, architecture design, RAAC, Reinforced Autoclaved Aerated Concrete