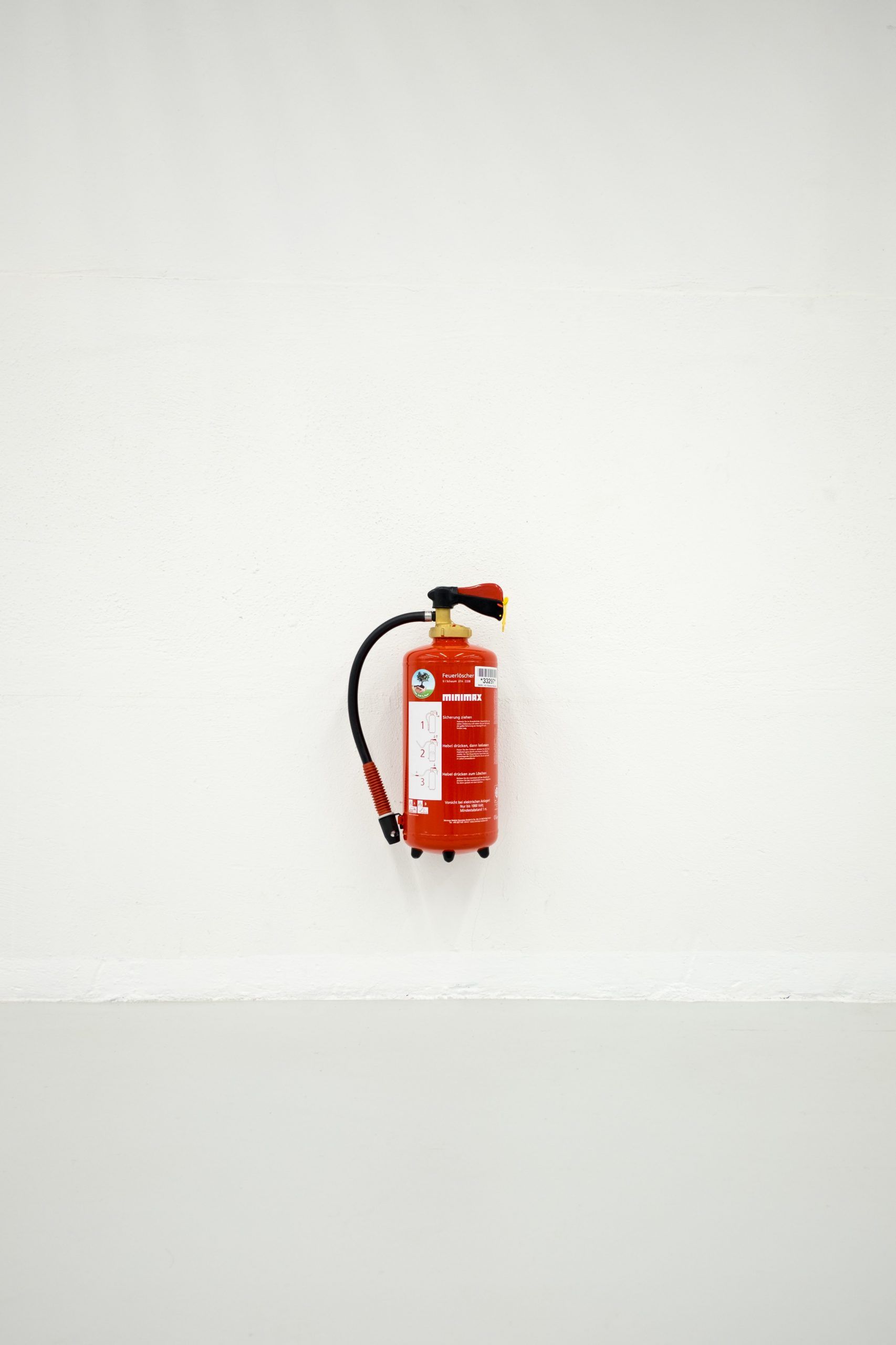
Five Ways To Improve Workplace Health And Safety Standards
Here at Munday + Cramer, we recently penned a piece on adhering to updated health and safety measures upon returning to work post-lockdown. As National Safety Month rolls on, however, it’s important to be clued into health and safety best practices, more generally, for when the pandemic is firmly in our rear-view mirrors. Working in facilities management, we’ve learned that there are myriad ways in which workplace health and safety can be improved. Some of these may seem startlingly obvious, and yet you’d be surprised at how few workplaces actually implement them. With that in mind, we’ve compiled an overview of key considerations in improving your workplace’s health and safety standards.
Have Your Employees Taught First Aid And Health & Safety
One of the very best things you can do as an employer is to pay for first aid and health and safety training for your employees. Whilst your business may have a designated health and safety officer, you can’t rely solely on them should an emergency occur. What if, for example, the health and safety officer is on annual leave when an accident occurs? It’s far better, then, that every team member has been properly taught at least basic first response techniques, so that they feel well equipped to deal with a situation. This knowledge can prove invaluable not only to your workplace but the wider world as well. Such training is recommended across all industries, but especially in the construction industries where risk forms an inherent part of the job.
Better Understand The Causes Of Fires At Work
Part of our remit as facilities managers is ensuring that a complex’s fire alarm testing is appropriately carried out. As such, we’ve learnt just how devastating fires can be, especially in the commercial sector. With the UK’s fire services attending fires in commercial buildings more than anywhere else, a better understanding of flammable risk in the workplace is imperative. Any equipment which could pose a fire hazard should be clearly signposted, and you should also educate your employees on the risk of using untested equipment, for example, or the risk that clutter often causes in starting a fire. When it comes to avoiding fires, human error is amongst the leading causes. The best form of mitigation, therefore, is always education.
Talk, Talk, Talk…
Communication is a vital aspect of so many areas of work, as well as life in general. We wouldn’t be able to work in facilities management if we didn’t place an emphasis on communication! Nowhere is it more crucial, however, in maintaining the personal health of your employees (both physical and mental). An honest, open and non-discriminatory dialogue between employer and employee surrounding mental health helps foster a better rapport and relationship. It prevents problems from building up and helps your employees avoid feeling like they’ve something to hide from their boss.
Encouraging candid and positive discourse on the topic of mental health can also help to better avoid accidents in the workplace. If you think about it, someone who is experiencing a bout of depression, for example, is going to be less aware and more prone to error – leaving an appliance on, let’s say. So, as you can see, it’s in everyone’s best interests that employees feel they can talk without fear of judgement or repercussions.
Provide Your Employees With The Appropriate Equipment
Fortunately, thanks to more stringent guidelines and regulations, there’s less ‘corner-cutting’ than there perhaps used to be, but it’s still essential that your employees are provided with appropriate, safe and tested equipment. Portable Appliance Testing (PAT) is a well-known example of testing that should be carried out in the workplace. It’s easy and simple to have done, and helps maintain the safety of electrical appliances being used throughout the workplace.
It’s not enough, though, to simply provide the equipment. It must be maintained beyond provision, especially in the case of machinery. A failure to carry out regular maintenance work is one of the leading causes of workplace injury. It can even be considered as negligent as the provision of faulty equipment in the first place. Testing should be well-documented so that no equipment ‘slips through the cracks’. When we’re contracted for facilities management work, we’re often shocked at how much of a facility’s equipment fails compliance tests. More often than not, however, it’s simply an innocent case of never having thought about it. Ignorance isn’t an excuse, though, and thorough equipment testing must form a part of your workplace practices.
Regularly Hold Meetings Regarding Health And Safety
A workplace is not a static thing; over time it grows and develops. With this evolution invariably comes new risks, concerns and potential hazards. All of these need to be discussed in the workplace. Beyond any training courses, employees should regularly be given the opportunity to voice any new concerns they may have. This, again, adds to the feeling of being valued in a workplace – that their voice matters. In turn, this will contribute to a more positive workplace environment, and thus greater productivity, as a result.
Upholding proper workplace safety standards is of paramount importance to both you, as an employer, and your employees. It simply cannot be skimped on. So, if you’d like to find out more about any of our services, whether it be our facilities management in Essex, or anything else, then get in touch! Contact Munday + Cramer today on 01245 326 200.